Makerbot® METHOD Carbon Fiber 3D Printer
Print Strong, Heat-Resistant Metal Replacement Parts
0.0 / 5
Makerbot® METHOD Carbon Fiber Edition 3D Printer Features
MakerBot Method Carbon Fiber Edition
Print carbon fiber reinforced nylon and other engineering-grade composite parts with three-dimensional strength and accuracy like never before on METHOD’s unique industrial desktop platform.
Strong, Heat-Resistant Metal Replacement Parts
Carbon fiber reinforced nylon is optimized for high strength, stiffness, and heat resistance making it ideal for structural applications and metal replacements.
- Excellent strength to weight ratio - 110 MPa TS - for lightweighting applications such as robotic end effectors
- Engineering-grade stiffness - 7600 MPa Tensile Modulus - for structural applications such as vehicular brackets and inspection gauges
- High heat resistance under load - 184°C HDT - for optimal under-hood and tooling applications
Superior Nylon Carbon Fiber Parts with METHOD
METHOD’s unique industrial feature set produces carbon fiber parts with superior three dimensional strength and accuracy
- METHOD’s Heated Chamber delivers parts that are strong and accurate.
- Outstanding surface finish that hides layer lines thanks to METHOD’s Ultra-Rigid Metal Frame.
- Print the most complex geometries including internal cavities with soluble support, or use breakaway support for faster print times.
- METHOD’s sealed filament bays help keep the material dry, resulting in better print quality and reliability, and METHOD’s pre-print spool drying feature allows for the recovery of oversaturated filament.
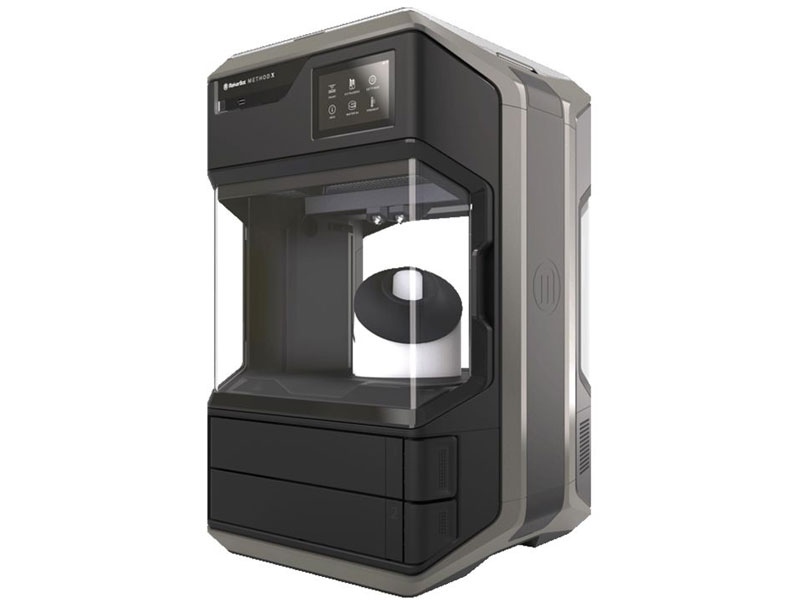
Stratasys Powered 3D Printer
Replace metal parts with 3D printed Carbon Fiber on METHOD
Print carbon fiber reinforced nylon and other engineering-grade composite parts with three dimensional strength and accuracy like never before on METHOD’s unique industrial desktop platform.
Why MakerBot METHOD Carbon Fiber?
Faster and more precise printing than ever before with manufacturing features you need:
- Heated Chamber
A Heated Chamber That Delivers Stronger Manufacturing-Grade Parts. - Advanced Materials
An Open Platform for Advanced Engineering Materials. - Part Accuracy
Guaranteed Part Accuracy and SR-30 Soluble Support. - Time Saving Workflow
Save Engineering Time with an Automated Workflow and CAD Integration.
Circulating Heated Chamber
Control the temperature and quality of every layer - not just the first. While heated build plates are effective at reducing warping, METHOD takes this further with full active heat immersion during the entire duration of the print.
METHOD 60°C Chamber | METHOD X 100°C Chamber
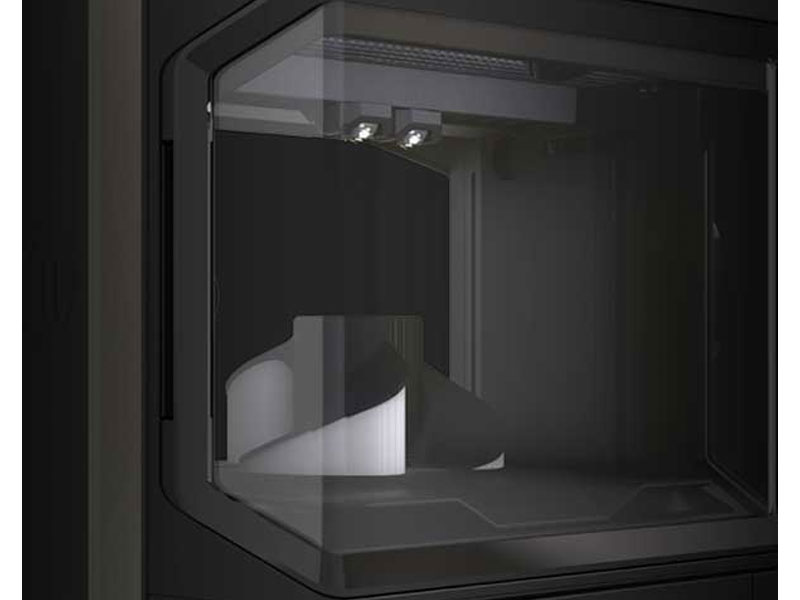
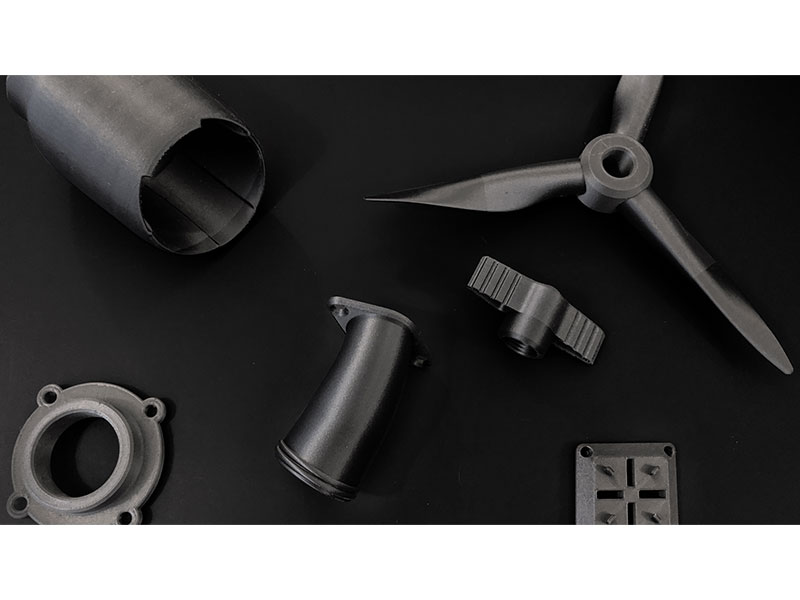
Metal Replacement Parts
Carbon fiber reinforced nylon is optimized for high strength, stiffness, and heat resistance making it ideal for structural applications and metal replacements.
- Excellent strength to weight ratio - 110 MPa TS - for lightweighting applications such as robotic end effectors
- Engineering-grade stiffness - 7600 MPa Tensile Modulus - for structural applications such as vehicular brackets and inspection gauges
- High heat resistance under load - 184°C HDT - for optimal under-hood and tooling applications
Nylon Carbon Fiber Parts
METHOD’s unique industrial feature set produces carbon fiber parts with superior three-dimensional strength and accuracy.
- METHOD’s Heated Chamber delivers parts that are strong and and accurate.
- An outstanding surface finish that hides layer lines thanks to METHOD’s Ultra-Rigid Metal Frame.
- Print the most complex geometries including internal cavities with soluble support, or use breakaway support for faster print
times. - METHOD’s sealed filament bays help keep the material dry, resulting in better print quality and reliability, and METHOD’s pre-print spool drying feature allows for the recovery of oversaturated filament.
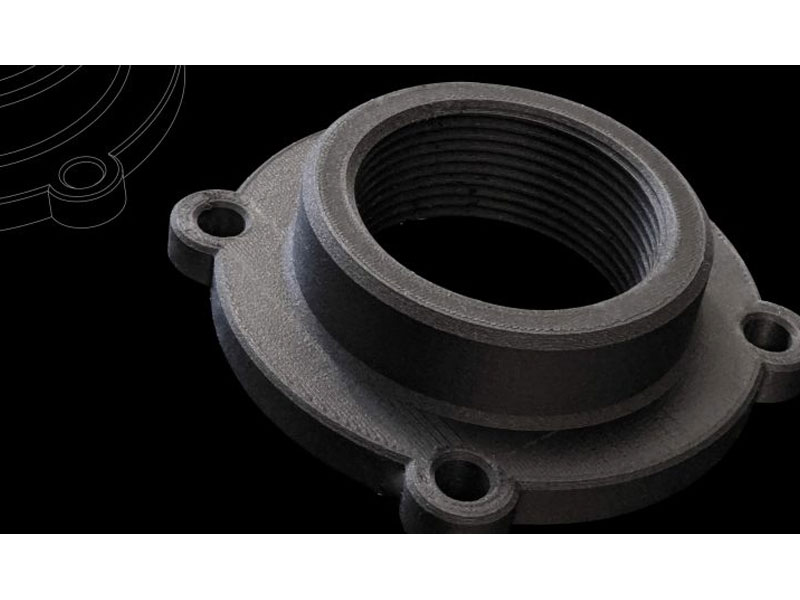
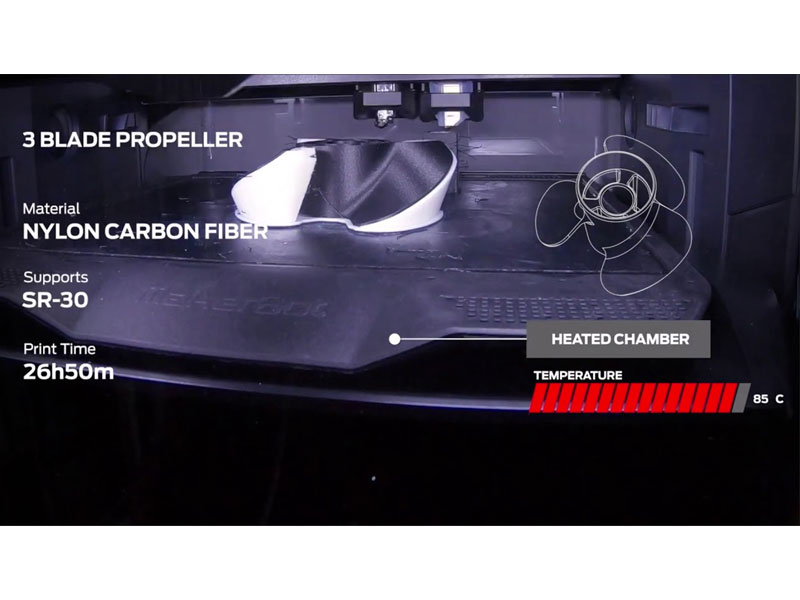
Disolvable Support System
Superior surface finish and unrestricted geometric freedom are paramount to delivering high quality printed parts.
Stratasys SR-30 ensures fast and effortless support removal without compromising part design or dimensional accuracy.
Stratasys SR-30 soluble support material provides two key benefits:
- Unrestricted geometric freedom (large overhangs, cavities, etc.)
- Superior print quality and surface finish
MakerBot METHOD Carbon Fiber Key Features:
Dual Performace Extruders
Featuring lengthened thermal cores, optimized torque, and an industry-leading sensor suite. Performance Extruders maximize material flow rate at high speeds while providing consistent and reliable extrusion across every layer.
Ultra-rigid Construction
A structurally-optimized metal frame runs the full length of the body to offset flexing. Less flexing means more consistent prints with better part accuracy and fewer failures.
Optimized Material Storage
Dry-Sealed Material Bays form a near-perfect seal to keep material free of damaging humidity. A suite of built-in sensors provides that your material is stored in its optimal environment—a feature previously only available in industrial 3D printers.
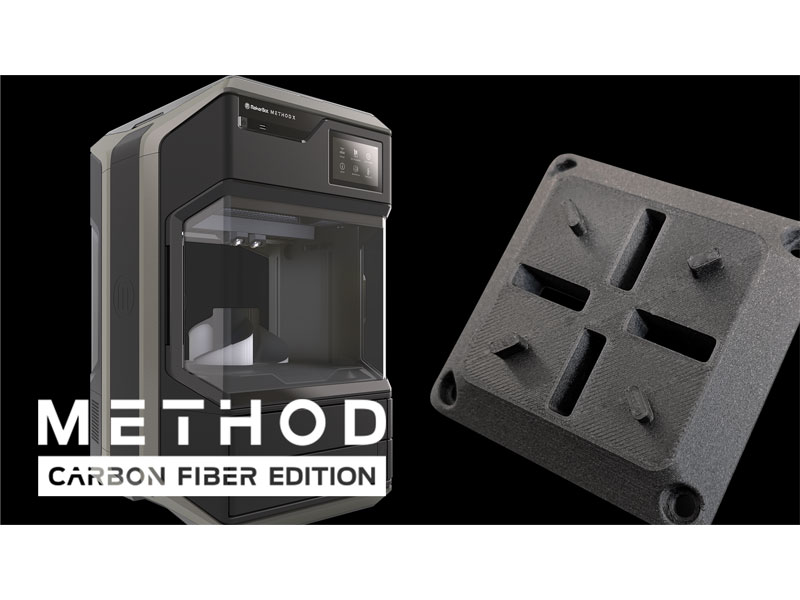
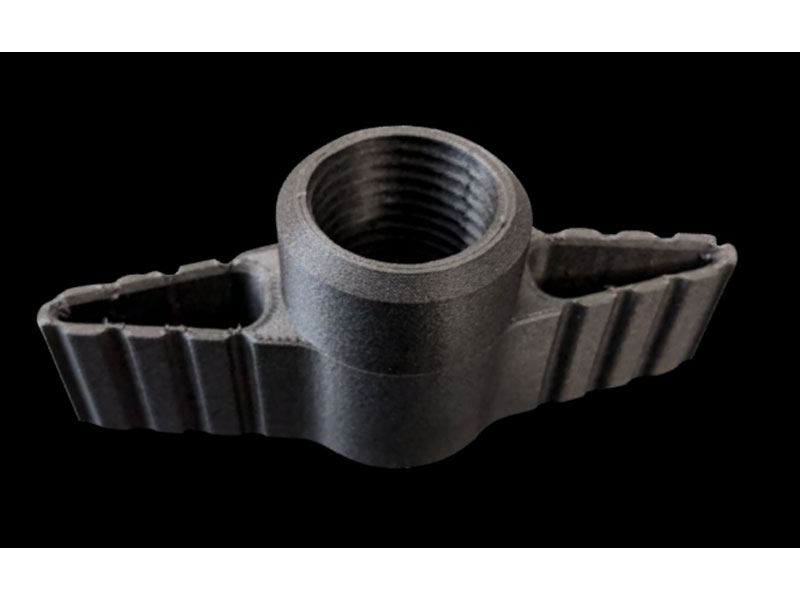
MakerBot Nylon Carbon Fiber
Carbon fiber reinforced nylon is optimized for high strength to weight ratio, stiffness, and heat resistance making it ideal for
structural applications and metal replacements.
STRENGTH TO WEIGHT
A formidable tensile strength of 110 Mpa makes MakerBot Nylon Carbon Fiber ideal for lightweighting metal parts such as robotic end effectors.
STIFFNESS
For applications that require parts hold their form with minimal flex - such as automotive brackets or inspection gauges, Nylon Carbon Fiber offers an impressive 7600 Mpa tensile modulus.
HEAT DEFLECTION
When exposed to heat other materials can deform under pressure. Nylon Carbon Fiber offers high heat deflection of 184°C making it great for higher temp under-hood and tooling applications.
- Accelerate Product Development
Put speed and control into your design cycles while reducing production costs to bring your products to market, fast. A project requiring 10 design iterations can be reduced to 4 days in-house using METHOD, as opposed to 40 days (including shipping) from an outsourced supplier. - Reduce Design Risk
Design mistakes found late in production can be exponentially more expensive than when found earlier in the product development cycle. METHOD allows your team to test and validate more prototypes with accuracy early and often; minimizing potential cost overruns later in production. - Reclaim the cost of development time
Put an end to frivolous tinkering, equipment upkeep, and stalled innovation at the cost of valuable design time. With the DNA and architecture of an industrial 3D printer, METHOD is built and extensively tested by MakerBot to print reliable prototypes—no tinkering or calibration required. - Low Total Cost of Ownership
From the purchase and installation to ongoing maintenance, materials, and support, METHOD is designed from the ground up to deliver industrial-quality performance at about one-third the first-year cost of ownership of an entry-level industrial 3D printer.
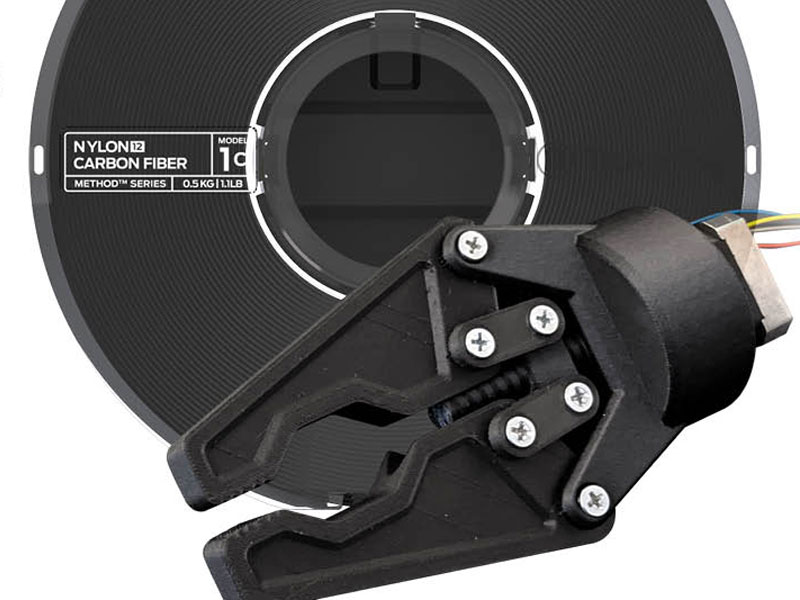
Are we missing the specification you need? Please go to our Contact Us page and submit your question to us, or call 1-877-284-7760
TECH SPECS | IMPERIAL | METRIC |
---|---|---|
Tensile Strength (ISO 527) | 16,000 psi | 110 Mpa |
Tensile Strength (ISO 527) | 1,102,000 psi | 7600 Mpa |
Strain at Yield (ISO 527) | 2% | 2% |
Heat Deflection Temperature (ASTM 648, 66 psi) | 360°F | 184°C |
FEATURE | METHOD CARBON FIBER | METHOD X CARBON FIBER |
---|---|---|
Specification | Print Carbon Fiber and a selection of polymers with the aid of a 60°C heated chamber | Print Carbon Fiber + the full range of engineering composites and polymers with a 110°C heated chamber |
Dimensional Accuracy | ±0.2mm (0.007in) | |
Heated Build Chamber Temperature | 60°C | 100°C |
Build Volume | Single Extrusion 19 L x 19 W x 19.6 H cm / 7.5 x 7.5 x 7.75 in Dual Extrusion 15.2 L x 19 W x 19.6 H cm / 6.0 x 7.5 x 7.75 in | |
Power Requirements | 100 - 240 VAC, 50/ 60 Hz, 400 W max 3.9A -1.6A | 100 - 240 VAC, 50/ 60 Hz, 800 W max 8.1A- 3.4 A |
Layer Resolution | 20-400 micron | |
MakerBot Materials | Nylon Carbon Fiber Precision Materials: PLA, Tough, PVA Specialty Materials: PETG | Nylon Carbon Fiber Precision Materials: PLA, Tough, PVA, ABS, Stratasys® SR-30 Specialty Materials: PETG |
Applications | Concept - Quick Prototypes - Fit Tests - Concept Iterations | Production - Manufacturing Tools - End-use Parts - Functional Prototypes |
Have a question that is not answered here? Please go to our Contact Us page and submit your question to us.
Looking for a quotation ? We would be happy to help by providing a quick response, inventory status, and Volume Level pricing, when available. Please fill out the form below and a representative will be in touch with you within hours to one business day to answer any questions and quote your request.
Product Details
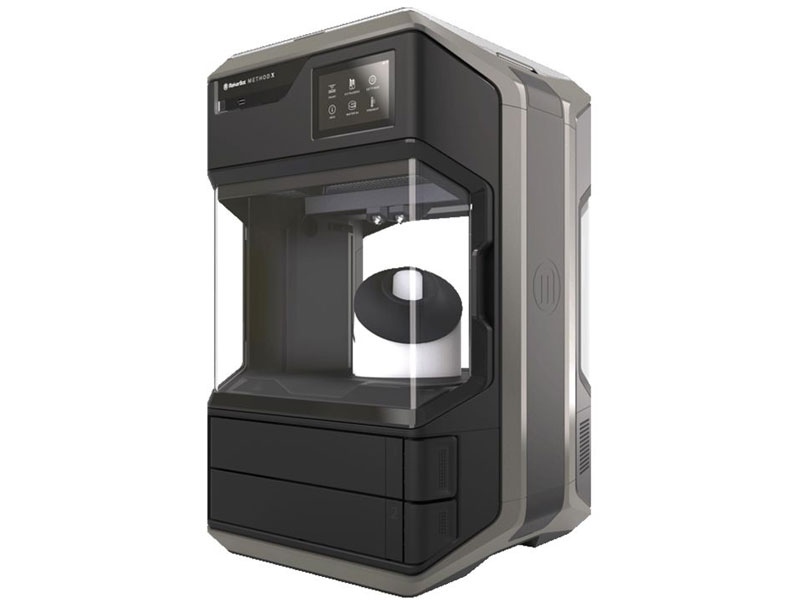
Stratasys Powered 3D Printer
Replace metal parts with 3D printed Carbon Fiber on METHOD
Print carbon fiber reinforced nylon and other engineering-grade composite parts with three dimensional strength and accuracy like never before on METHOD’s unique industrial desktop platform.
Why MakerBot METHOD Carbon Fiber?
Faster and more precise printing than ever before with manufacturing features you need:
- Heated Chamber
A Heated Chamber That Delivers Stronger Manufacturing-Grade Parts. - Advanced Materials
An Open Platform for Advanced Engineering Materials. - Part Accuracy
Guaranteed Part Accuracy and SR-30 Soluble Support. - Time Saving Workflow
Save Engineering Time with an Automated Workflow and CAD Integration.
Circulating Heated Chamber
Control the temperature and quality of every layer - not just the first. While heated build plates are effective at reducing warping, METHOD takes this further with full active heat immersion during the entire duration of the print.
METHOD 60°C Chamber | METHOD X 100°C Chamber
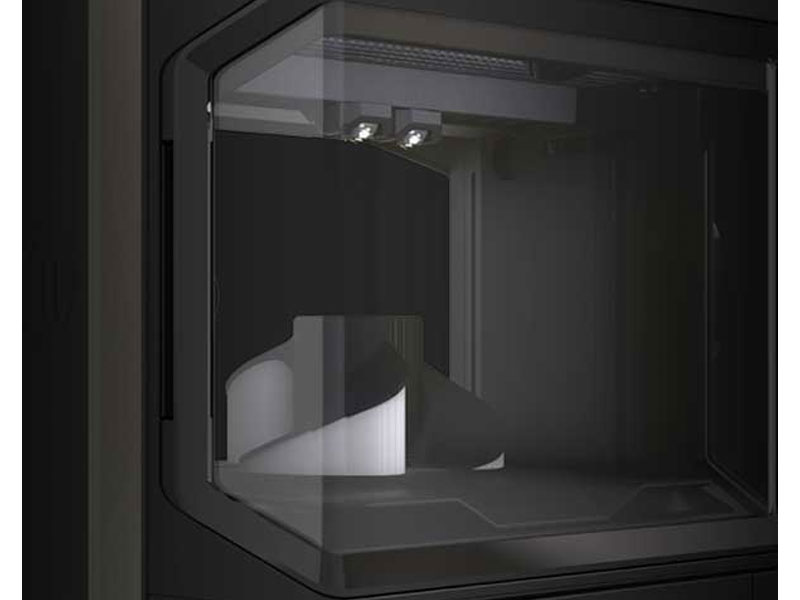
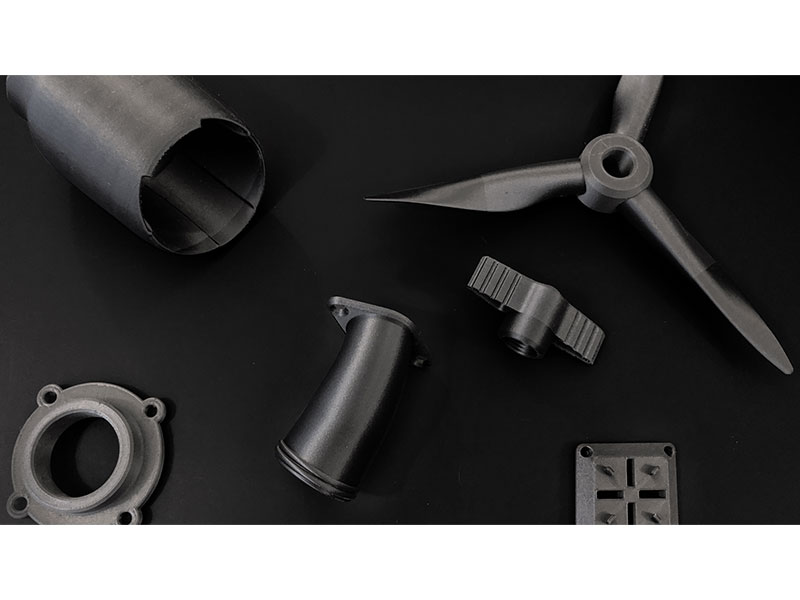
Metal Replacement Parts
Carbon fiber reinforced nylon is optimized for high strength, stiffness, and heat resistance making it ideal for structural applications and metal replacements.
- Excellent strength to weight ratio - 110 MPa TS - for lightweighting applications such as robotic end effectors
- Engineering-grade stiffness - 7600 MPa Tensile Modulus - for structural applications such as vehicular brackets and inspection gauges
- High heat resistance under load - 184°C HDT - for optimal under-hood and tooling applications
Nylon Carbon Fiber Parts
METHOD’s unique industrial feature set produces carbon fiber parts with superior three-dimensional strength and accuracy.
- METHOD’s Heated Chamber delivers parts that are strong and and accurate.
- An outstanding surface finish that hides layer lines thanks to METHOD’s Ultra-Rigid Metal Frame.
- Print the most complex geometries including internal cavities with soluble support, or use breakaway support for faster print
times. - METHOD’s sealed filament bays help keep the material dry, resulting in better print quality and reliability, and METHOD’s pre-print spool drying feature allows for the recovery of oversaturated filament.
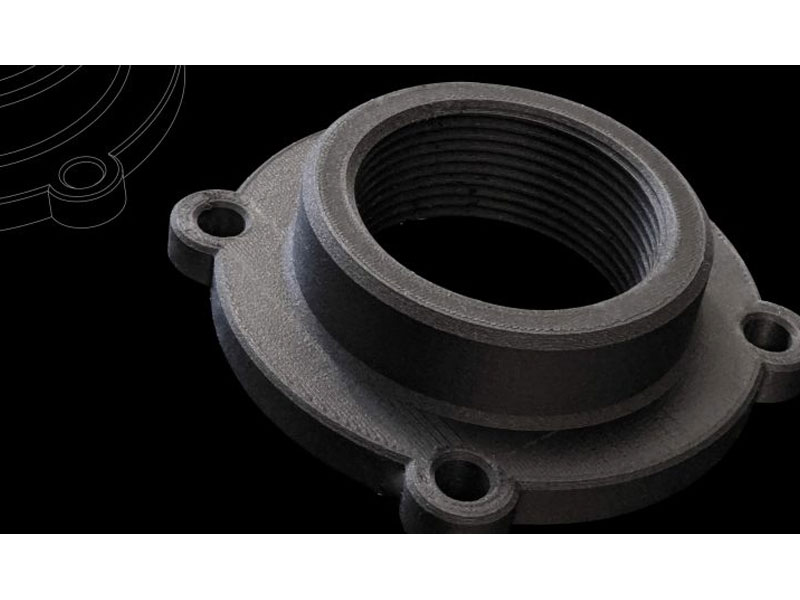
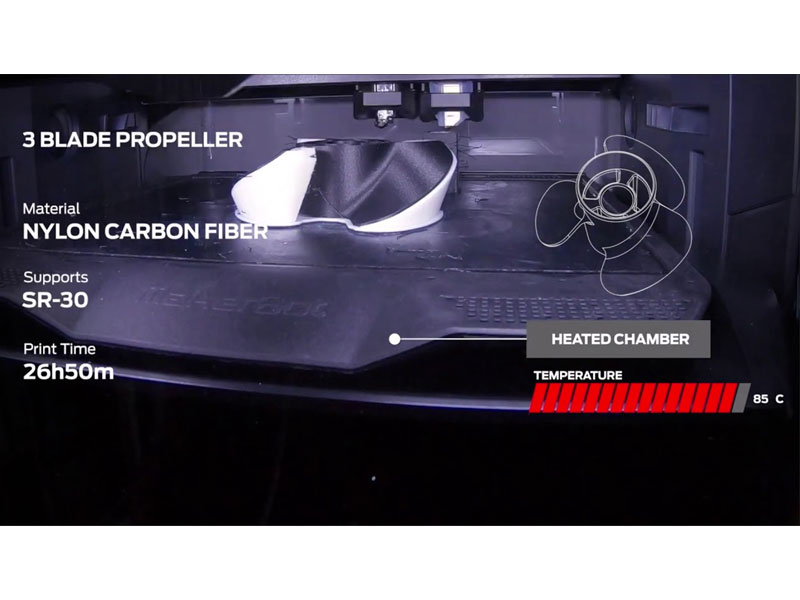
Disolvable Support System
Superior surface finish and unrestricted geometric freedom are paramount to delivering high quality printed parts.
Stratasys SR-30 ensures fast and effortless support removal without compromising part design or dimensional accuracy.
Stratasys SR-30 soluble support material provides two key benefits:
- Unrestricted geometric freedom (large overhangs, cavities, etc.)
- Superior print quality and surface finish
MakerBot METHOD Carbon Fiber Key Features:
Dual Performace Extruders
Featuring lengthened thermal cores, optimized torque, and an industry-leading sensor suite. Performance Extruders maximize material flow rate at high speeds while providing consistent and reliable extrusion across every layer.
Ultra-rigid Construction
A structurally-optimized metal frame runs the full length of the body to offset flexing. Less flexing means more consistent prints with better part accuracy and fewer failures.
Optimized Material Storage
Dry-Sealed Material Bays form a near-perfect seal to keep material free of damaging humidity. A suite of built-in sensors provides that your material is stored in its optimal environment—a feature previously only available in industrial 3D printers.
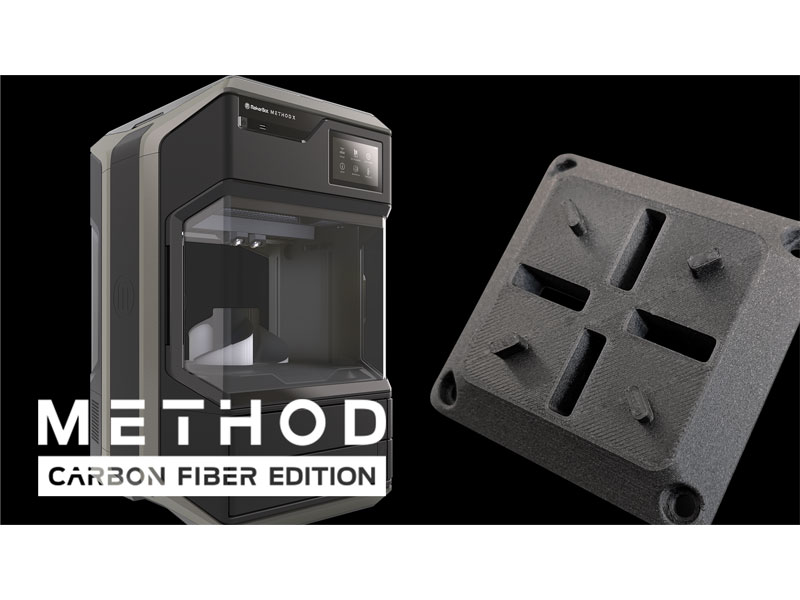
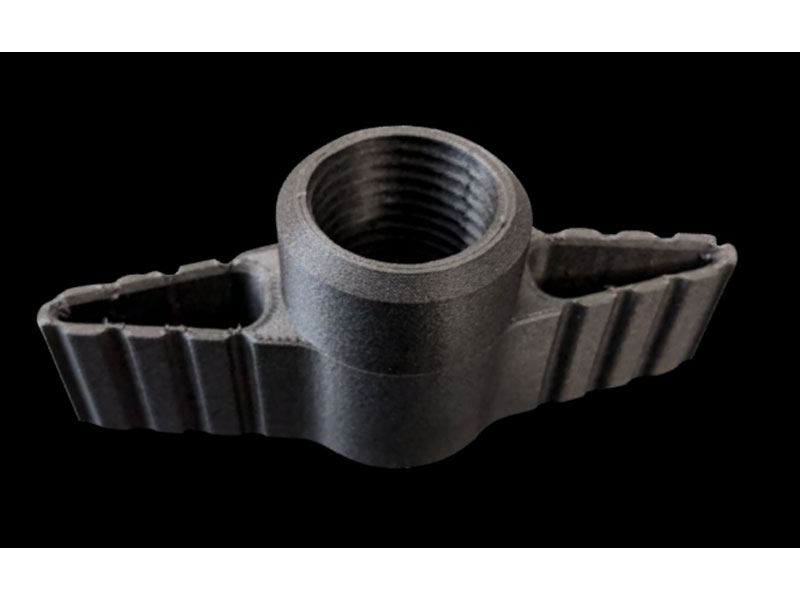
MakerBot Nylon Carbon Fiber
Carbon fiber reinforced nylon is optimized for high strength to weight ratio, stiffness, and heat resistance making it ideal for
structural applications and metal replacements.
STRENGTH TO WEIGHT
A formidable tensile strength of 110 Mpa makes MakerBot Nylon Carbon Fiber ideal for lightweighting metal parts such as robotic end effectors.
STIFFNESS
For applications that require parts hold their form with minimal flex - such as automotive brackets or inspection gauges, Nylon Carbon Fiber offers an impressive 7600 Mpa tensile modulus.
HEAT DEFLECTION
When exposed to heat other materials can deform under pressure. Nylon Carbon Fiber offers high heat deflection of 184°C making it great for higher temp under-hood and tooling applications.
- Accelerate Product Development
Put speed and control into your design cycles while reducing production costs to bring your products to market, fast. A project requiring 10 design iterations can be reduced to 4 days in-house using METHOD, as opposed to 40 days (including shipping) from an outsourced supplier. - Reduce Design Risk
Design mistakes found late in production can be exponentially more expensive than when found earlier in the product development cycle. METHOD allows your team to test and validate more prototypes with accuracy early and often; minimizing potential cost overruns later in production. - Reclaim the cost of development time
Put an end to frivolous tinkering, equipment upkeep, and stalled innovation at the cost of valuable design time. With the DNA and architecture of an industrial 3D printer, METHOD is built and extensively tested by MakerBot to print reliable prototypes—no tinkering or calibration required. - Low Total Cost of Ownership
From the purchase and installation to ongoing maintenance, materials, and support, METHOD is designed from the ground up to deliver industrial-quality performance at about one-third the first-year cost of ownership of an entry-level industrial 3D printer.
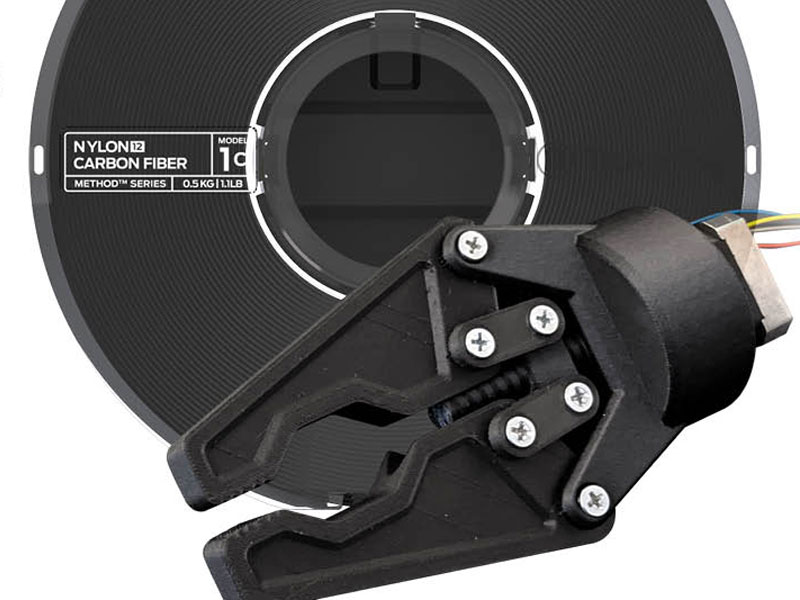
Product Specifications
Are we missing the specification you need? Please go to our Contact Us page and submit your question to us, or call 1-877-284-7760
TECH SPECS | IMPERIAL | METRIC |
---|---|---|
Tensile Strength (ISO 527) | 16,000 psi | 110 Mpa |
Tensile Strength (ISO 527) | 1,102,000 psi | 7600 Mpa |
Strain at Yield (ISO 527) | 2% | 2% |
Heat Deflection Temperature (ASTM 648, 66 psi) | 360°F | 184°C |
FEATURE | METHOD CARBON FIBER | METHOD X CARBON FIBER |
---|---|---|
Specification | Print Carbon Fiber and a selection of polymers with the aid of a 60°C heated chamber | Print Carbon Fiber + the full range of engineering composites and polymers with a 110°C heated chamber |
Dimensional Accuracy | ±0.2mm (0.007in) | |
Heated Build Chamber Temperature | 60°C | 100°C |
Build Volume | Single Extrusion 19 L x 19 W x 19.6 H cm / 7.5 x 7.5 x 7.75 in Dual Extrusion 15.2 L x 19 W x 19.6 H cm / 6.0 x 7.5 x 7.75 in | |
Power Requirements | 100 - 240 VAC, 50/ 60 Hz, 400 W max 3.9A -1.6A | 100 - 240 VAC, 50/ 60 Hz, 800 W max 8.1A- 3.4 A |
Layer Resolution | 20-400 micron | |
MakerBot Materials | Nylon Carbon Fiber Precision Materials: PLA, Tough, PVA Specialty Materials: PETG | Nylon Carbon Fiber Precision Materials: PLA, Tough, PVA, ABS, Stratasys® SR-30 Specialty Materials: PETG |
Applications | Concept - Quick Prototypes - Fit Tests - Concept Iterations | Production - Manufacturing Tools - End-use Parts - Functional Prototypes |
Product Manuals
Frequently Asked Questions
Have a question that is not answered here? Please go to our Contact Us page and submit your question to us.